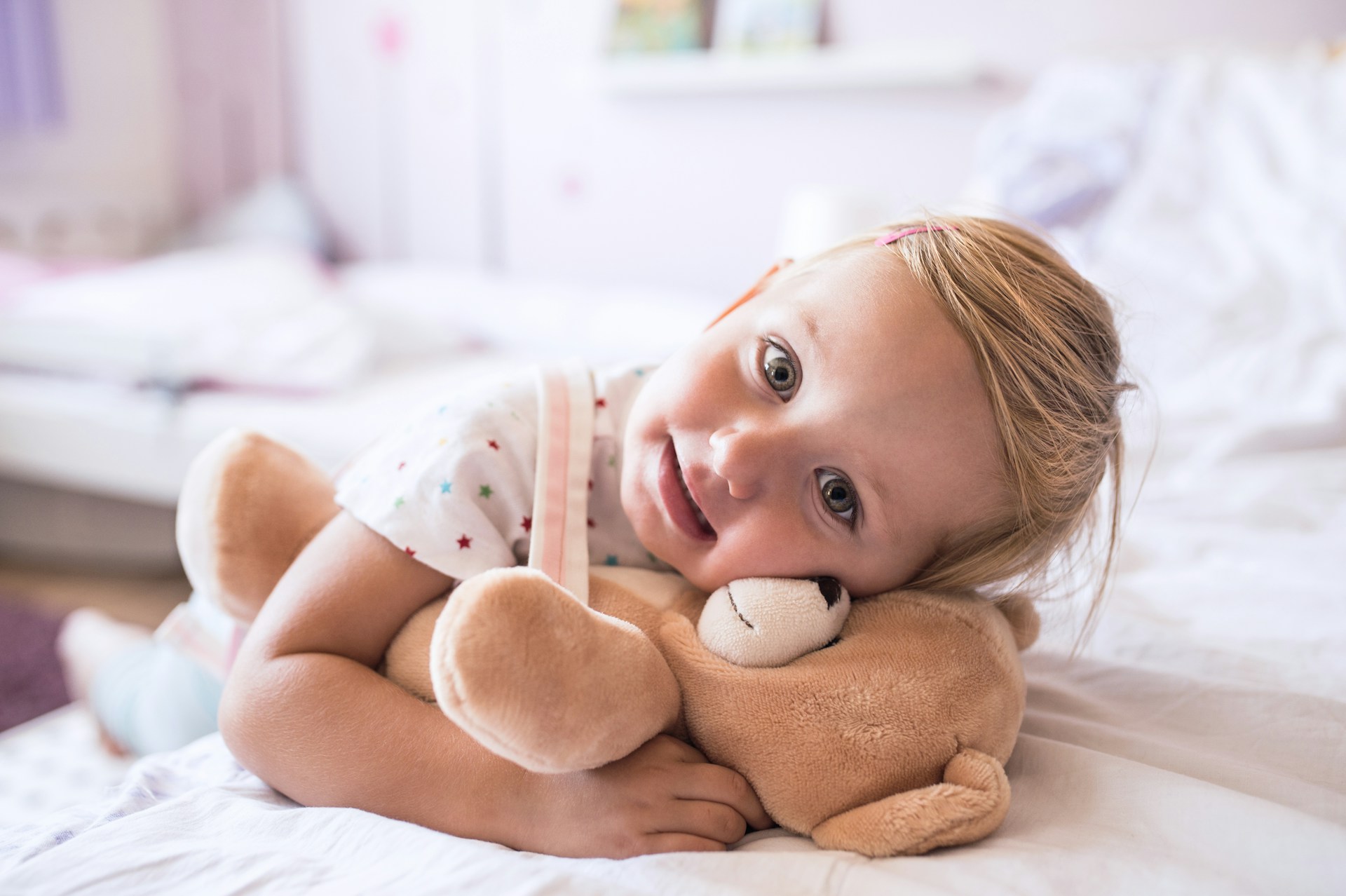
Understanding Dental Implants
Dental implants have become the gold standard for tooth replacement, offering a solution that mimics the function and appearance of natural teeth. Unlike dentures or bridges, implants are surgically anchored into the jawbone, providing a stable and long-lasting foundation for crowns, bridges, or even complete denture systems.
Key Components of a Dental Implant
- Implant Fixture: A titanium or zirconia screw that acts as the root of the tooth, embedded into the jawbone.
- Abutment: A connector piece that attaches to the implant fixture, rising above the gumline.
- Prosthetic Crown: The artificial tooth that mimics the appearance and function of a natural tooth.
The Traditional Path: Conventional Dental Implants
Historically, dental implants have been crafted using traditional manufacturing methods. This involves a combination of manual casting, milling, and molding to create the necessary components. While effective, these methods can be time-consuming and may lack the level of precision achievable with modern technologies.
Limitations of Traditional Implants
- Customization Challenges: Creating implants that perfectly fit an individual’s anatomy requires significant manual adjustment.
- Time-Consuming Process: Multiple steps and prolonged manufacturing times can delay treatment completion.
- Material Constraints: Limited material options can affect the implant’s biocompatibility and longevity.
Rise of 3D Printing in Dentistry
Enter 3D printing, a technological marvel that has permeated various industries, including healthcare. In dentistry, 3D printing offers unparalleled precision, customization, and efficiency, making it an ideal candidate for revolutionizing dental implants.
What is 3D Printing?
3D printing, or additive manufacturing, involves creating three-dimensional objects by layering materials based on digital models. This process allows for intricate designs and customized solutions that are difficult or impossible to achieve with traditional manufacturing methods.
Types of 3D Printing Technologies in Dentistry
- Stereolithography (SLA): Uses a laser to cure liquid resin into hardened plastic in a layer-by-layer fashion.
- Selective Laser Sintering (SLS): Utilizes a laser to sinter powdered material, binding it together to create a solid structure.
- Digital Light Processing (DLP): Similar to SLA but uses a digital light projector for faster manufacturing.
- Binder Jetting: Deposits a liquid binding agent onto a powdered material, joining the particles selectively.
How 3D-Printed Dental Implants Are Made
The creation of 3D-printed dental implants involves several meticulously coordinated steps, ensuring precision and customization at every stage.
1. Digital Scanning and Imaging
The process begins with capturing detailed images of the patient’s oral anatomy using digital scanning technologies such as:
- Intraoral Scanners: Provide real-time, high-resolution 3D images of the mouth.
- Cone Beam Computed Tomography (CBCT): Offers comprehensive imaging of the jawbone and surrounding structures.
2. Digital Design and Modeling
Using specialized software, dental professionals design the implant to perfectly fit the patient’s anatomy. This digital workflow allows for:
- Customization: Tailoring the implant’s shape, size, and angle to match the patient’s unique needs.
- Simulation: Predicting the implant’s behavior and integration within the jawbone.
3. Material Selection
Biocompatible materials are crucial for ensuring the implant’s success. Common materials include:
- Titanium: Widely used for its strength and biocompatibility.
- Zirconia: Offers a metal-free alternative with aesthetic advantages.
- Biodegradable Polymers: Used in temporary scaffolds that facilitate natural bone growth.
4. 3D Printing
The selected material is precisely deposited layer by layer to construct the implant. Advanced printers can achieve microscopic accuracy, ensuring that the implant replicates the digital model flawlessly.
5. Post-Processing
After printing, implants undergo various post-processing steps such as:
- Cleaning: Removing any residual powder or material.
- Heat Treatment: Enhancing material properties and implant strength.
- Surface Finishing: Smoothing surfaces to promote better integration with bone tissue.
6. Quality Control and Sterilization
Rigorous quality checks ensure that the implant meets all necessary standards. Sterilization processes are employed to make the implant safe for surgical use.
Advantages of 3D-Printed Dental Implants
3D printing brings numerous benefits to dental implantology, transforming both patient experiences and clinical outcomes.
1. Customization and Precision
Each implant is tailored to the patient’s specific anatomical requirements, ensuring a perfect fit. This level of customization reduces the risk of implant failure and enhances the overall success rate.
2. Speed and Efficiency
3D printing significantly reduces the time required to manufacture implants. What once took weeks can now be achieved in days, accelerating the treatment timeline and minimizing patient discomfort.
3. Cost-Effectiveness
By streamlining the production process and reducing manual labor, 3D-printed implants can be more affordable without compromising quality.
4. Material Versatility
3D printing allows for the use of a diverse range of materials, offering options that best suit the patient’s needs and preferences, including metal-free alternatives for those with metal sensitivities.
5. Improved Biocompatibility and Integration
Advanced materials and precise manufacturing techniques enhance the implant’s compatibility with bone tissue, promoting faster and more effective osseointegration (the process by which the implant fuses with the bone).
6. Reduced Waste
Additive manufacturing is inherently more material-efficient, as it only uses the necessary amount of material to build the implant, minimizing waste compared to subtractive manufacturing methods.
Current Applications and Success Stories
The integration of 3D printing in dental implants has already shown promising results in various clinical settings.
1. Guided Implant Surgery
3D-printed guides are used to assist surgeons in accurately placing implants, ensuring optimal positioning and alignment. This not only enhances precision but also reduces surgical time and patient discomfort.
2. Immediate Loading Implants
With the speed of 3D printing, implants can sometimes be loaded immediately upon placement, allowing patients to have functional teeth within a single appointment.
3. Full-Arch Replacements
For patients requiring multiple implants or full-arch replacements, 3D printing facilitates the creation of complex structures that integrate seamlessly with existing bone structures.
Challenges and Considerations
While 3D-printed dental implants offer numerous advantages, there are challenges and considerations that need to be addressed to ensure their successful adoption.
1. Regulatory Approvals
Navigating the regulatory landscape is essential. Implants must meet stringent safety and efficacy standards set by authorities like the FDA (Food and Drug Administration) or EMA (European Medicines Agency).
2. Material Limitations
While the range of materials is expanding, ensuring biocompatibility and durability remains paramount. Ongoing research is essential to develop new materials that meet these criteria.
3. Cost of Equipment
The initial investment in high-quality 3D printers and software can be substantial, potentially limiting access for smaller practices.
4. Training and Expertise
Dental professionals must acquire the necessary skills to operate 3D printing equipment and integrate digital workflows into their practice effectively.
5. Long-Term Data
As a relatively new technology, long-term studies are needed to fully understand the longevity and performance of 3D-printed implants over decades.
6. Intellectual Property Concerns
With digital designs being a core component, protecting intellectual property and ensuring the integrity of designs is crucial to prevent unauthorized replication.
The Future Landscape
The future of 3D-printed dental implants is bright, with continuous advancements poised to further enhance their functionality and accessibility.
1. Integration with AI and Machine Learning
Artificial Intelligence (AI) can optimize implant design processes by analyzing vast datasets to predict successful outcomes, leading to even more personalized treatments.
2. Bioprinting and Tissue Engineering
Advancements in bioprinting could enable the creation of implants that incorporate living cells, promoting natural tissue growth and even regeneration of surrounding bone and gum tissues.
3. Sustainability Initiatives
Future 3D printing technologies may focus on eco-friendly materials and energy-efficient processes, aligning dental innovations with sustainable practices.
4. Enhanced Connectivity and Tele-Dentistry
With the rise of remote consultations and tele-dentistry, digital workflows enabled by 3D printing can facilitate seamless collaboration between patients, dentists, and specialists across different locations.
5. Affordability and Accessibility
As technology matures, the cost of 3D printers and materials is expected to decrease, making advanced dental implants more accessible to a broader population.
6. Smart Implants
The integration of sensors and IoT (Internet of Things) technology into implants could enable real-time monitoring of implant health, detecting issues like inflammation or improper integration early on.
Conclusion
3D-printed dental implants represent a significant leap forward in tooth replacement technology. By harnessing the power of additive manufacturing, dentistry is moving towards more personalized, efficient, and effective treatments. While challenges remain, the continued collaboration between dental professionals, technologists, and researchers promises to refine and enhance this innovative approach. As we look to the future, 3D-printed implants stand at the forefront of dental innovation, offering patients a brighter, healthier, and more comfortable path to restored oral health.
FAQs
1. Are 3D-printed dental implants safe?
Yes, 3D-printed dental implants are made from biocompatible materials such as titanium and zirconia, which are well-tolerated by the body. However, it's essential to ensure that they are manufactured under strict quality control standards.
2. How long do 3D-printed dental implants last?
When properly maintained, 3D-printed dental implants can last several decades, similar to traditional implants. The longevity depends on factors like oral hygiene, lifestyle, and regular dental check-ups.
3. Is the 3D printing process painful?
The 3D printing process itself is not painful as it occurs outside the patient. The surgical procedure for implant placement is comparable to traditional methods, with similar levels of anesthesia and post-operative care.
4. Can anyone get a 3D-printed dental implant?
Most individuals who are candidates for traditional dental implants can also opt for 3D-printed alternatives. However, a thorough dental examination is necessary to determine suitability based on bone density, oral health, and overall health conditions.
5. How much do 3D-printed dental implants cost?
The cost can vary based on factors like materials, complexity of the case, and geographic location. While 3D printing can reduce some costs through efficiency, the initial investment in technology may influence pricing.
Embracing 3D-printed dental implants means stepping into a future where tooth replacement is not only more efficient but also tailored to individual needs, enhancing both functionality and aesthetics. As this technology continues to evolve, it holds the promise of transforming dental care, offering patients improved outcomes and a better quality of life.